2017-2018 SDSM&T Academic Catalog [ARCHIVED CATALOG]
Materials and Metallurgical Engineering Department
|
|
Return to: Undergraduate Studies
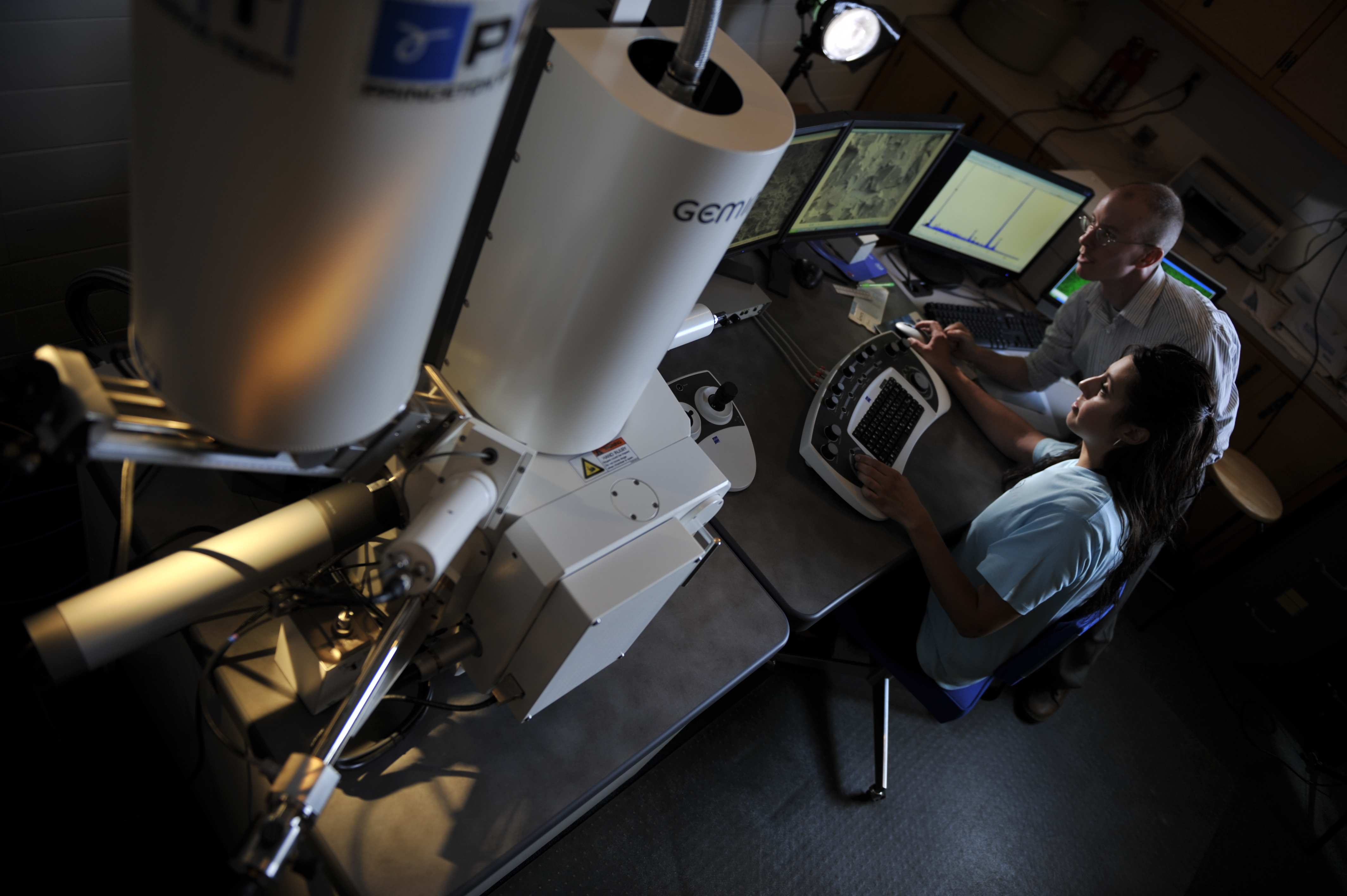
Contact Information
Dr. Michael K. West
Department of Materials and Metallurgical Engineering
Mineral Industries 101
(605) 394-1283
E-mail: Michael.West@sdsmt.edu
Faculty
Douglas W. Fuerstenau Professor Kellar; Professor Salem; Associate Professors Cross, West, and Widener; Assistant Professors Crawford, Jasthi, and Safarzadeh; Research Scientist Meruga; Adjunct Professors Bendler, Kustas, and Medlin; Distinguished Professor Emeritus Han; Professor Emeriti Howard and Stone.
Materials and Metallurgical Engineering
Materials and metallurgical engineering is the branch of engineering that develops and supplies the materials for virtually every other engineering field. Three-fourths of all elements are metals, so metals play a vital role in nearly every aspect of modern life. Metallurgical engineers transform the Earth’s mineral resources into finished products by extracting metals from ores, producing ceramics from metal compounds, and fabricating composite structures.
Modern materials are exotic and so are the methods of producing them. Metallurgy is based upon the principles of chemistry, physics, and mathematics. These sciences provide an understanding of the methods of metal production processes and the behavior of materials. In addition to familiar materials such as steel, aluminum, copper, glass, gold, and silver, metallurgical engineers produce many exotic materials such as metals with shape memories, ultrahigh-purity materials for integrated circuits, materials for surgical implants, ceramics for space vehicles, nano-scale metal particles and superconductors. There are 3 areas of specialization in metallurgical engineering: mineral processing, extractive metallurgy, and materials engineering. Mineral processors concentrate ores and recycled materials so that extractive metallurgists can produce pure, high-quality metals and non-metallics for use by materials engineers who transform these materials into the marvels of our advanced civilization, ranging from space craft to thin diamond films. Metallurgical engineers are actively involved in nanotechnology and the production and utilization of nano-scale materials.
Advances made by metallurgical and material engineers make advances possible in other engineering fields. This happens because virtually every engineering field is in constant search of higher-performing materials. Metallurgical engineers are responsible for the production of materials and also for the evaluation of metals, ceramics, and polymer-based composites. The evaluation of materials includes tests to determine strength, hardness, toughness, corrosion behavior, and many other properties. It is the role of metallurgical engineers to develop processing methods to create materials with specific and exacting properties for every conceivable application.
The primary source for materials continues to be extracted as ores and petroleum from the Earth. However, recycled materials are an increasingly important material source for metallurgical engineers.
Materials and metallurgical engineers are employed throughout the nation and the world.
The Bachelor of Science Degree in Metallurgical Engineering is accredited by the Engineering Accreditation Commission of ABET, http://www.abet.org.
Materials and Metallurgical Engineering Laboratories
Laboratory facilities in metallurgical engineering are equipped for instruction in mineral processing, chemical metallurgy, physical metallurgy, and mechanical metallurgy. Sample preparation facilities, laser light scattering particle size analyzers, gravitational separation equipment, laser Doppler particle size and zeta potential measurement equipment are available for mineral and materials processing. Induction melting and vacuum furnaces, fluidized-bed reactors, corrosion potentiostat, contact angle goniometer, and high pressure autoclaves are available for chemical metallurgy. X-ray diffraction spectrometer, Fourier transform infrared spectrometer, Raman spectrometer, Langmuir-Blodgett trough, metallographs, atomic force microscope, controlled atmosphere furnaces, quantitative image analyzer, scanning and transmission electron microscopes, universal testing machine (MTS), Charpy impact testing machine, and micro hardness, Rockwell and Vickers hardness testers are available for measuring material performance.
Modern laboratory facilities for welding and joining are available within the metallurgical engineering laboratories. These facilities include traditional joining (fusion welding) as well as advanced joining (friction stir joining) equipment.
Co-Curricular Opportunities
Co-curricular opportunities in blacksmithing, glassblowing and the artistic aspects of metallurgy are also available. Where appropriate, these co-curricular activities are integrated into the metallurgical engineering curriculum.
The program hosts the summer Research Experiences for Undergraduates (REU) Site: Back to the Future! The REU Site is sponsored by the National Science Foundation.
Return to: Undergraduate Studies
|